Flexography

Smart press design for cost-effective production
- Highly modular concept enables very fast installation and start-up
- Automatically opening and closing bearings for plate cylinder equipped with a pre-load system for maximum stability. Deck design avoiding deflection and tilting
- The joint action of the two component doctor blade chamber, the smart inking and easy cleaning systems increase press uptime
- Dual technology nozzles in the tunnel ensure optimum drying performance
- Operator viewing platform on catwalk for web monitoring of the print result and a convenient access to CI drum ensure higher machine productivity and availability
- Automatic face-to-face winders
- Wide range of standard options
- Available as 8-color and 10-color press.
Superior print quality
- Superior output quality with a wide range of substrates types and thicknesses
- Consistent and repeatable printing quality with solvent-based and water-based ink printing
- Anti vibration bearing design. Automatic opening/closing system for plate cylinders equipped with a pre-load system for maximum stability
- Continuously monitored viscosity control, fully integrated in the inking and cleaning system
- Bridge tunnel with dual technology nozzles. High efficiency drying for very low solvent retention on substrates.
Ergonomic, easy to operate and waste saving
- Flexibility and sustainability within a compact design
- User-friendly access to all print decks for maintenance and cleaning
- Low height to load sleeves and aniloxes, easy front access to plate, easy change of doctor blades
- Design of intra-colour dryer for easy access and cleaning
- Energy savings due to efficient drive system and ventilation
- Connectivity features to enable access to production data from remote services.
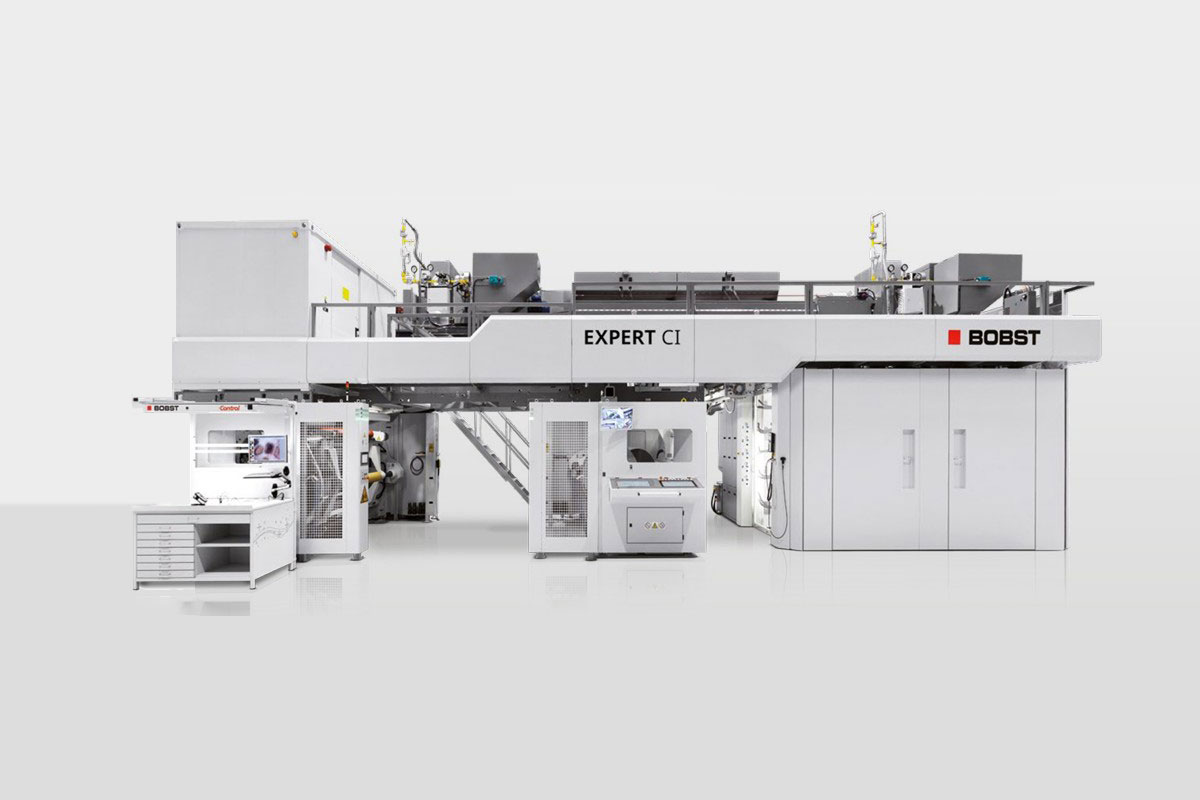
Exclusive innovations for unrivalled performance
- Minimum waste of substrate and consumables at start-up and job changes with smartGPS or smartSET exclusive systems for registration and impression setting
- smartFLO inking system and chamber doctor blade delivering predictable, stable and controlled printing results with all ink types
- triLOCK bearing system with high torque mechanism replacing manual locking
- Full Surface Matrix intercolor dryer preventing substrate stretching
- oneECG for optimized results with 7-color ECG process
- Hybrid, dual technology tunnel. Energy saving due to efficient drive system and ventilation
- Fully automatic bi-directional reel splice at machine production speed. Winders’ energy recovery solution
- Compact footprint with face-to-face winders.
Exceptional printing flexibility
- Select from 4 printing systems:
- Solvent-based printing
- Water based printing
- E-beam printing
- Extended Color Gamut printing (ECG)
- smartGPS off-line fully automatic system for registration and impression setting or smartSET-press semi-automatic set-up system
- Modular extendable configuration of the drying tunnel
- Customizable for specific product requirements – downstream flexo units, gravure printing units and turning bars for reverse printing.
Connected and automated for maximum uptime
- Accurate process automation for minimized waste, increased cost efficiency and easy manufacturing
- Connectivity features to enable access to production data from remote services
- IoT including Predictive Maintenance empowering the operator to change wear parts before they fail.
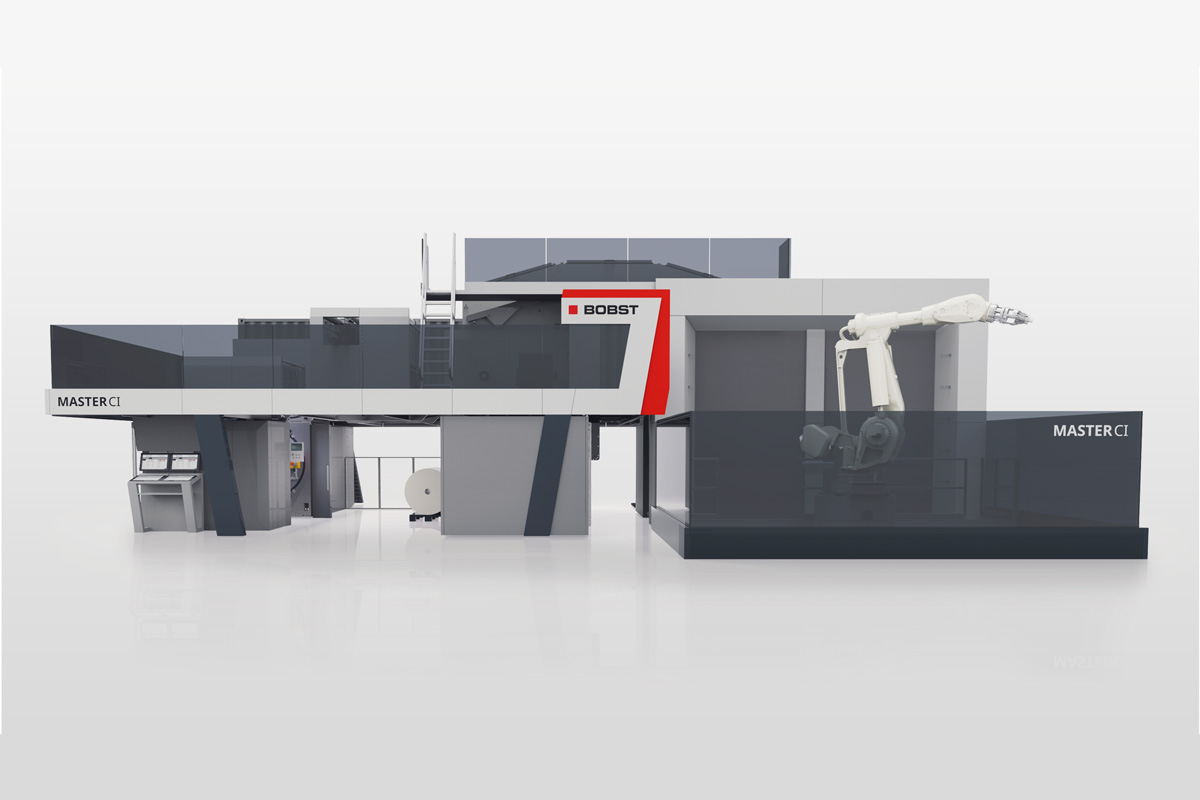
Ground-breaking technologies for exceptional productivity
- Modular design for fast installation and commissioning in less than 4 weeks
- Unique press architecture enabling to either manually change the sleeves or to automatically replace all shafted elements and the sleeves of the print decks using the smartDROID system
- smartCLEAN II on-board washing for fast cleaning of print units. Individual wash-up for doctor-blade change, speeding up the press make-ready, from the operator’s side. Combined with the new smartCOL, a color matching system that measures the LAB values before printing, it minimizes ink consumption and facilitates machine handling
- Exclusive combined shaft and shaftless function in one winder design for fast and easy handling irrespective of run lengths and production requirements
- Automatic splice at high speed in less than 2 minutes from loading of reel to splice ready, guaranteeing minimal substrate waste
- smartTHREAD for web threading from unwinder to rewinder in less than 3 min
- New generation smartGPS II allows digital proofing and offline quality check and preparation of print tools
- High production speed, up to 800 m/min.
Repeatable and consistent print quality & sustainable operation
- Optimized machine configuration and exclusive technical solutions for maximum performance:
- New print decks with automatic bearing block solutions for maximum stability
- New concept for plate cylinder and anilox roller shafts, combined with sleeve-cylinder handling
- Direct torque drives on multiple sections
- Quick change and easy to handle two-piece doctor blade chamber
- New CI-Cleaner system cleaning the CI drum during production
- Energy saving modules for sustainable operation.
Digitalized production workflow and connected services
- Job Recipe Management System for a digitalized production workflow from file to finished product with creation of a digital twin of the produced reels
- smartTOOL fully automatic tool management system
- smartCAL automatic calibration and monitoring of all main production and service data
- Predictive maintenance enabling the operator to change wear parts before they fail
- Connected Services.