Window Patching
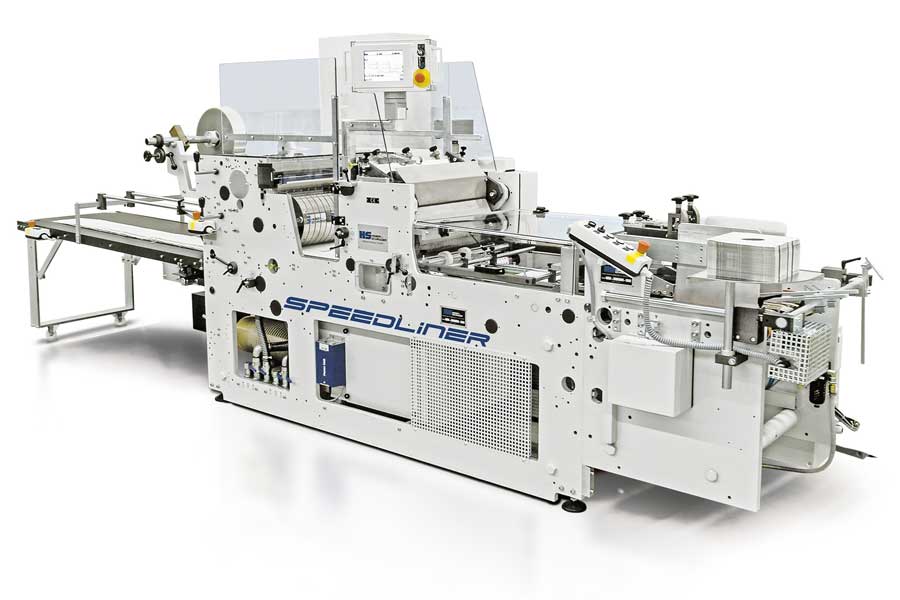
SOLID OUTPUT
- Up to 36,000 blanks per hour at ideal use of space (1 lane production)
REDUCED DOWNTIME AND INCREASED PRODUCTIVITY
- Patented feeder teach-in function and electronic friction control
PRECISION
- Outstanding foil/liner positioning due to an improved blank transfer system
STABLE AND ROBUST
- Heavy duty cross cutting system, smoother foil/liner cutting with less jam risk
LIFETIME DURABILITY
BEST-IN-CLASS SERVICE AND SUPPORT
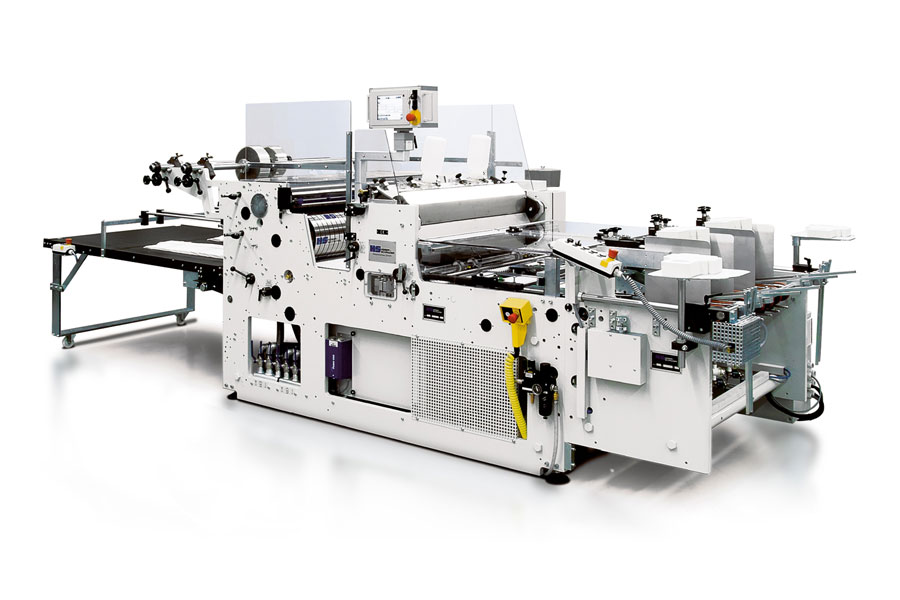
SOLID OUTPUT
● Up to 72,000 blanks per hour (2 lane production)
● Smooth operation even for film material with critical static load through high performance static discharge system
REDUCED DOWNTIME AND INCREASED PRODUCTIVITY
● Gluing unit with full splash guard and 2-minute integrated cleansing system
● Excellent flatness of the blanks (even when curved) thanks to patented mono-suction belt
● Best application tolerance for the film, both in running and lateral direction
● Maintenance-free air suction system, (no vacuum channels or filters)
● Standstill times for reel change can be eliminated by a patented H+S splicer system (option), constant web tension during operation and reel change is provided by automatically controlled brakes and dancer rollers
PRECISION
● Outstanding foil/liner positioning due to an improved blank transfer system
STABLE AND ROBUST
● Heavy duty cross cutting system, smoother foil/liner cutting with less jam risk
QUICK AND EASY SET-UP
● Electronically controlled time belt feeder series, automatic compensation of the feeder timing in case of changing friction or belt wear, feeding length adjustment via teach-in-button with only one single blank
● Film length adjustment via digital input, and during machine operation
● Automatic position alignment of cutting cylinders, suction cylinder in case of cycle change of film length reduces set-up times, defined machine stop position avoids operation errors and reduces standstill times
USER AND MATERIAL FRIENDLY
● Chemically nickel-plated, tooled steel inserts for suction holes (optional), cleanser-resistant, minimal wear, minimal risk of scratches on the film
● Laterally movable delivery ensures better ergonomics when mounting heavy film reels or working on the cutting station
● Intelligent adjustment-free jam monitoring at the chain station, safe and time saving
LIFETIME DURABILITY
BEST-IN-CLASS SERVICE AND SUPPORT
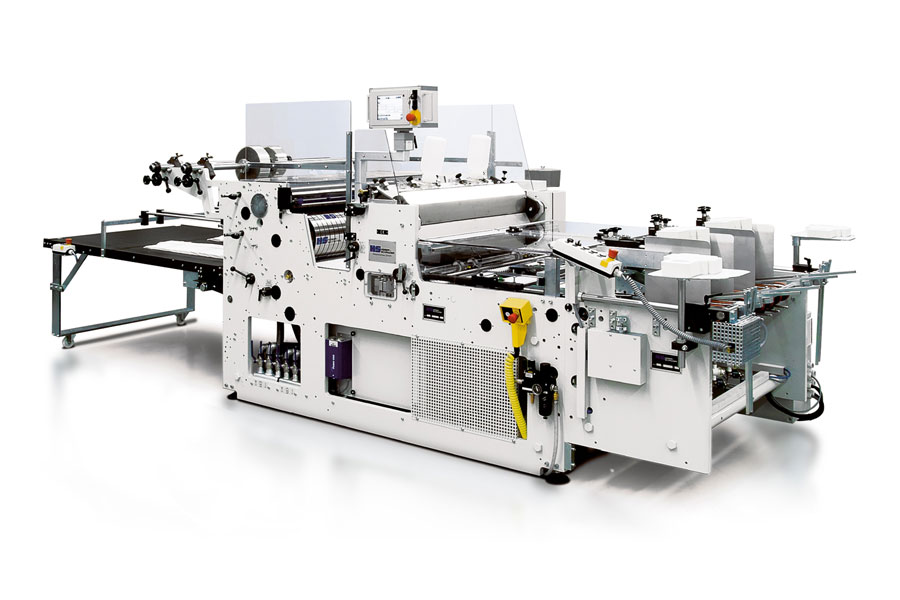
OPERATING PANEL
- Picture supported library for repeat orders
- Production statistics and, optional, production data acquisition
- Picture supported error messages
- Picture supported help system
- Modem connection for service and updates
- Automatic maintenance alerts
MINIMAL WEAR AND REDUCED MAINTENANCE EFFORT
- Chemically nickel-plated suction cylinder, tooled steel inserts for suction holes, cleanser-resistant, minimal risk of scratches on the film
- Latest generation drive technology: servo motors drive all rotating elements and are power consumption-optimized and maintenance-free
REDUCED DOWNTIME AND INCREASED PRODUCTIVITY
- Excellent flatness of the blanks (even when curved) thanks to patented mono-suction belt
- Gluing unit with full splash guard and 2-minute integrated cleansing system
- Standstill times for reel change can be eliminated by a patented H+S splicer system (option), constant web tension during operation and reel change is provided by automatically controlled brakes and dancer rollers
MASTER FEEDER
- Up to 4 different run modes
- Ideal feeding technology for each blank form and each type of material
- Electronically controlled, with lifter-free timing and automatic self-monitoring
- Feeding length adjustment via Teach-In button