Metallizers
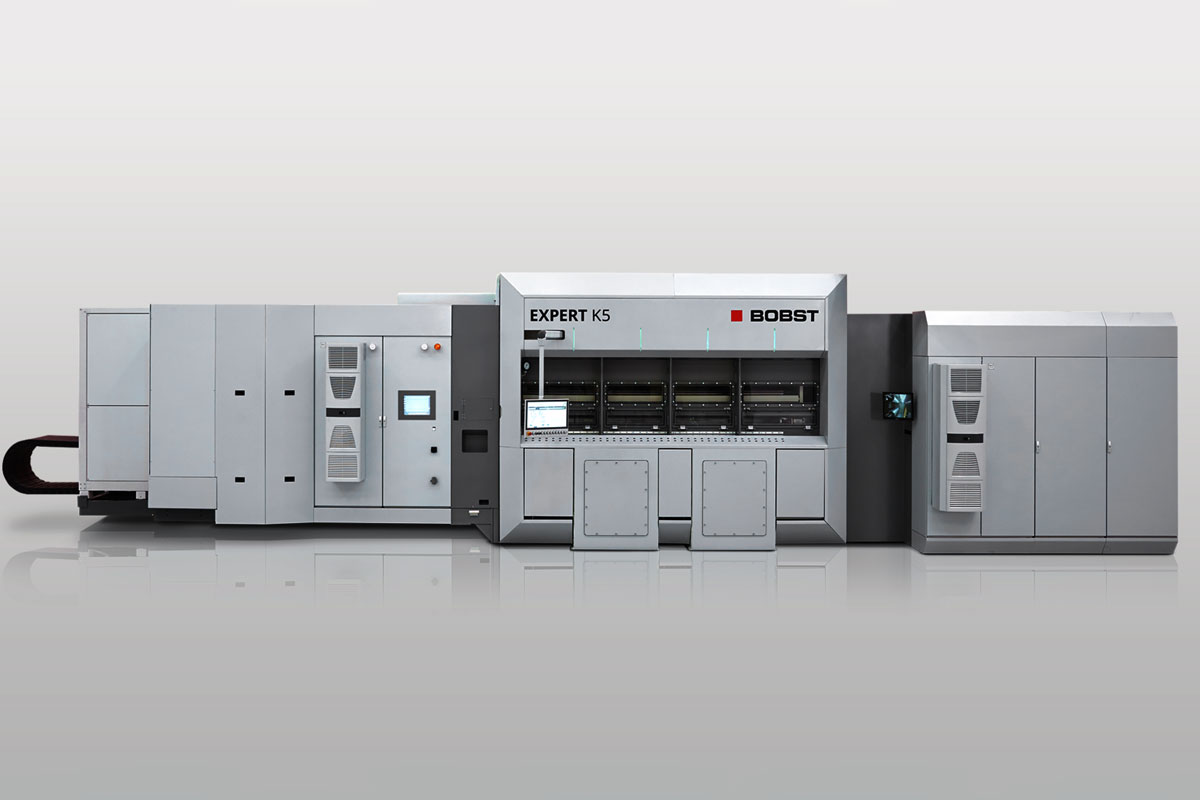
Outstanding performance
- High speed metallizing
- Ability to house increased roll diameters up to 1,270 mm
- Largest coating window in the industry with improved collection efficiency of 16%
- Largest diameter coating drum in the industry at 700 mm
- Easy to operate with an Automatic Sequential Control (ASC) system
- Incorporates the BOBST renowned winding mechanism.
Energy saving and waste reduction
- ECO mode reduces energy consumption by up to 50% during standby
- Film Save mode minimises amount of film waste to less than 400 m per roll
- 15% more aluminium deposited on the web
- Reduced carbon footprint.
Lowest production costs in the market
- Reduced production cycle increasing number of rolls per day
- 20% savings in production costs
- Maximum machine uptime
- Total Cost of Ownership reduced by up to 25% compared to competitors.
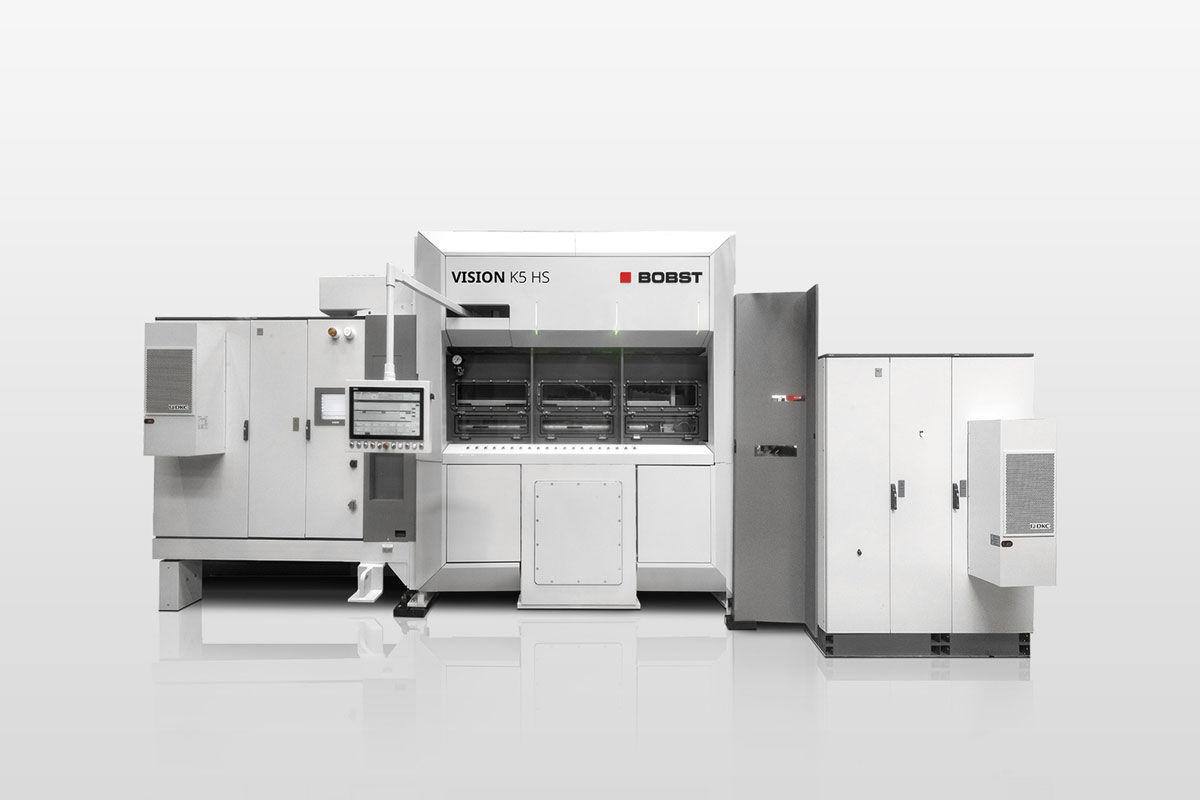
Total flexibility
- High speed metallizing
- Designed to handle a variety of film types including heat sensitive, thin gauge and sustainable substrates
- Ideal for converters of PE
- Incorporates the BOBST renowned winding mechanism.
Improved cooling
- Largest coating drum in the industry at 700 mm
- Increased cooling efficiency for PE & low SIT films
- Largest coating window in the industry with improved collection efficiency
- Less aluminium consumption and improved boat life.
High performance
- 100 mm full staggered boat arrangement
- Improved coating uniformity at high speeds
- Minimum roller contact
- Designed for careful handling of heat sensitive substrates.

With oneBARRIER, BOBST has undertaken a design and testing project that is creating industrially viable recycle-ready mono-material ultra-high and high barrier duplex and triplex substrates for packaging designers as alternatives to non-recyclable metallized polyester film. Developed with leading industry partners, the family of BOBST oneBARRIER sustainable solutions to date includes PrimeCycle, comprising EVOH and topcoat-free transparent AlOx-based or opaque AluBond-based full PE mono-substrates, and FibreCycle, a mono-material high-barrier paper-based structure coated with functional layers that can be recycled in the existing paper stream.
The BOBST & Partners oneBARRIER solutions are the outcome of joint process and equipment development and testing. The advantages for converters are manyfold:
- Integrated package solution: process-machine-output in one flow
- Knowledge of both coating and vacuum metallizing equipment technology and processes from a single supplier
- Different kinds of raw material specifications, coating, and adhesive chemicals
- Guaranteed barrier properties of the full structures (pre-coat + metallization + post coat + eventually lamination)
The result is a fully reliable process to consistently produce top quality polyolefin-based or paper-based recycle-ready ultra-high or high barrier packaging, with faster time-to-market from day one.
The oneBARRIER equipment package comprises the EXPERT K5 vacuum metallizer and the oneBARRIER EXPERT COATER or the one BARRIER MASTER COATER coating lines, depending on the converter’s productivity needs. oneBARRIER solutions web widths range from 1300 to 2900 mm.
EXPERT K5 vacuum metallizer
- Perfectly accurate web handling on all paper and film types and thicknesses, including the new generation of sustainable substrates (BOPE, MDO PE, CPE) and low temperature heat sealable BOPP films
- Handles AlOx deposition process for production of clear film and AluBond metallizing process for production of opaque film
- High cooling capacity with largest diameter coating drum in the industry at 700 mm
- Largest coating window in the industry with improved collection efficiency of 16%.
oneBARRIER COATER coating lines
- Perfectly accurate web handling on all paper and film types and thicknesses, including the new generation of sustainable substrates (BOPE, MDO PE, CPE) and low temperature heat sealable BOPP films
- Excellent coating profile consistency with water-based and solvent-based coatings
- Single or multiple coating heads as option
- Modular trolley-type configuration allowing for future changes of application technology
- Hybrid dual technology dryer or full floatation dryer with option for additional tunnel sections.