Cast Film Lines
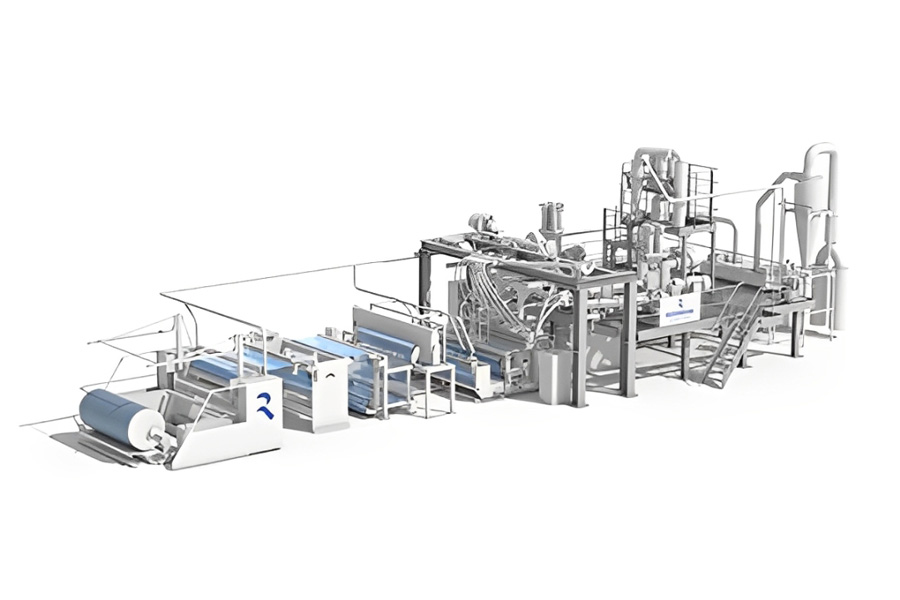
Tailor-made cast film lines for customized CPP and CPE film.
Cast polypropylene films (CPP film) are the standard used for packaging film in the food and industrial sectors.
CPP films offer the best solution regarding transparency (appearance), printability, metallization, and sealability.
Value CPP Ultra Wide lines cover the entire bandwidth of these applications. The line concept is tailor-made for a custom film product and to meet specific customer requirements.
A melt is produced by an extruder from a PP granulate. Up to 5 individual layers are superimposed by a feedblock and expanded in a flat die to widths up to 7 m. The downstream casting process includes a cooled roll to finish the film to the required properties.

Cast film lines for film with optimized barrier properties.
Ensuring a secure global food supply is one of the most important challenges facing humanity. To achieve this, reducing food waste in the supply chain is essential.
Sophisticated and sustainable barrier films and packaging solutions play a key role in reducing food losses, ensuring hygienic packaging of sensitive goods, improving customer convenience and at the same time being as resource-efficient as possible.
With our sophisticated, fully integrated and automated Value Cast barrier cast film lines, we offer the film and packaging industry a safe and proven solution.
The system concepts meet our customers’ requirements for reproducible and traceable quality with digital solutions for process and performance monitoring, but also with high-precision and reliable system components.
Starting with high-precision and reliable metering systems, followed by wear-resistant and pressure-constant multi-purpose extruders for excellent melt quality, ensuring a constant supply to the core components of such a line – the co-extrusion feedblock and die.
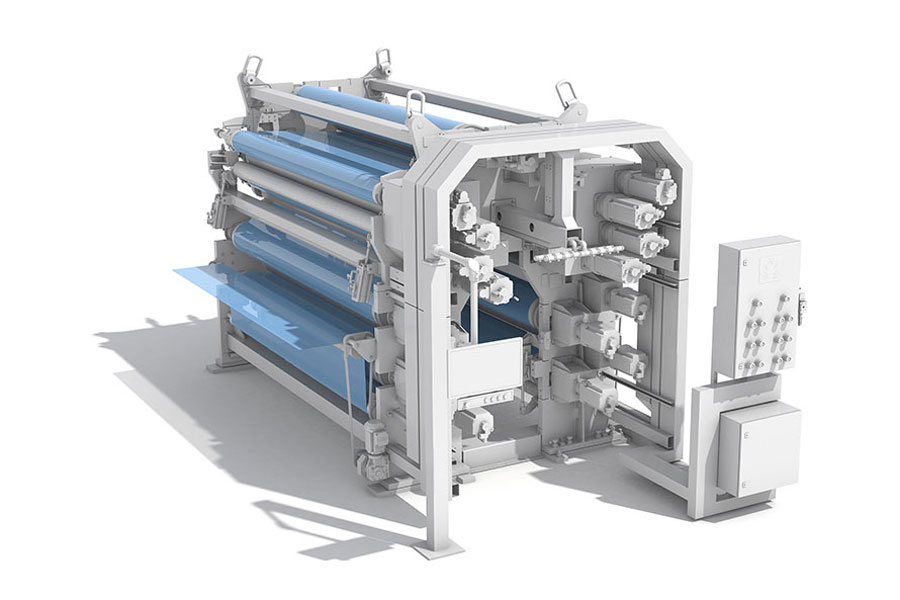
Stretching units for breathable cast film.
From diapers to medical protective clothing to films for roofing, cast films have a wide range of uses in applications that require breathable films.
Applications, industries and line concept. Value Cast Hygiene / Industry equipment can be used to produce breathable films. For breathable films, inline MDO units are used for stretching. Combined with the possibility of direct extrusion of fillers, this results in highly economical production.
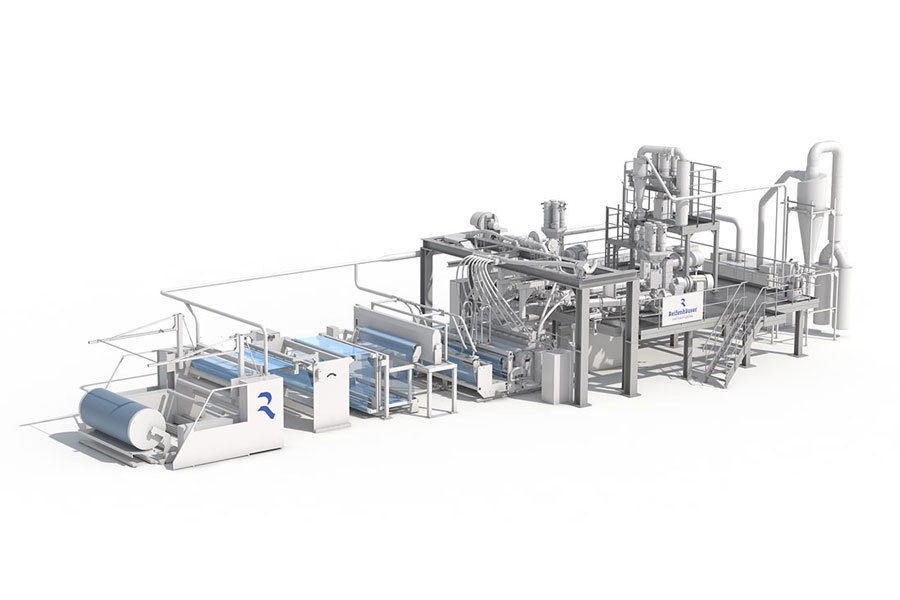
CPP/CPE cast film line with fast ROI, high OEE, and very short time to market.
CPP films are ideal for packaging films in the medical and consumer goods sectors, and in industry. Your benefits: Cast films are highly transparent and feature good sealability and printability.
The enormous bandwidth of requirements for film production often culminate in customized solutions. The alternative is a modular concept, i.e. an assembly kit containing proven components. This is the basic idea behind our Value lines.
Value Line incorporates proven Reifenhäuser quality. The use of field-proven, high-availability assemblies and perfectly coordinated project teams and processes ensure extremely short delivery and assembly times.
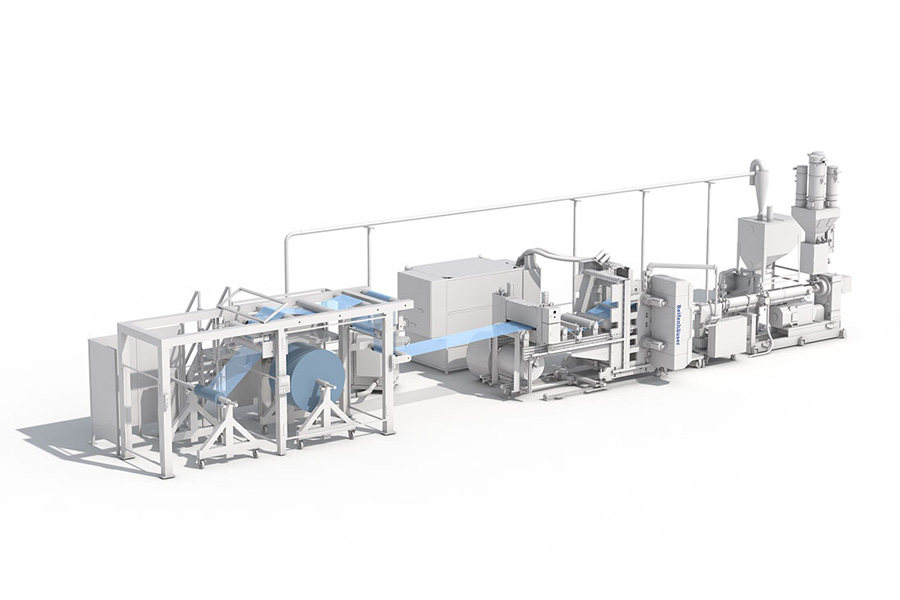
High-performance polishing stacks to process PP/PS film.
Polystyrene (PS) and polypropylene (PP) is widely used for the production of packaging for the dairy industry, drinking cups and MAP packaging. For the requirements of these packaging, films with one to five layers are processed.
Applications, industries and line concept.
Drinking cups, yogurt cups, margarine tubs, meat packaging and salad bowls are often produced from polystyrene (PS) as well as polypropylene (PP).
Value Sheet PS/PP lines enable the production of PP/PS packaging under the highest quality standards.
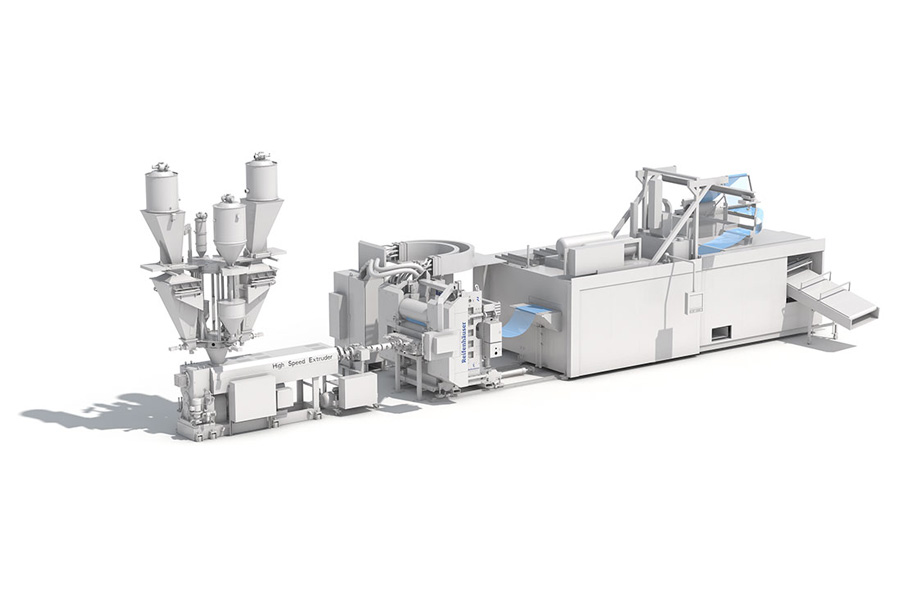
Polishing stack to feed film to the thermoformer in an inline process.
Value Sheet inline lines can be integrated into new or existing production chains and fit any thermoforming machine.
Value Sheet inline lines allow the production of films and products to the highest quality standards. Inline lines are used in a wide range of applications such as yogurt or drinking cups, meat and cheese packaging.
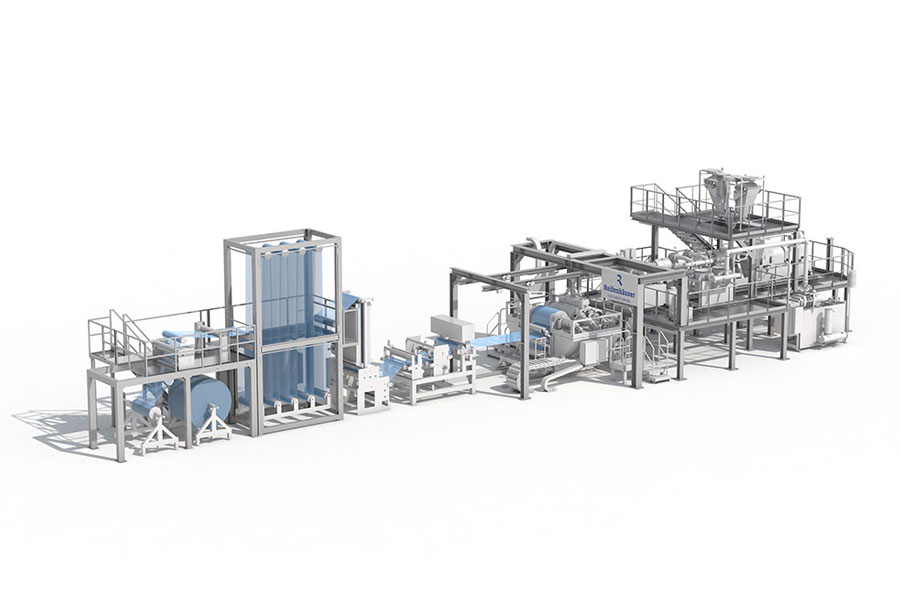
Tailor-made polishing stacks to process PET and PLA.
PET is used for a wide range of applications: from food packaging to blisters and folding cartons.
PET films are the basis for packaging a wide range of products such as fruit, vegetables and meat. In addition, there are other applications, for example in the packaging of medicine or electronic components, in which the raw material G-PET is used.
PLA is replacing more and more PET films, especially in the field of food packaging. So it requires a high flexibility of your line.
Value Sheet PET/PLA calendering lines cover the complete range of these applications. The respective line concept is tailor-made for the specific film product and the individual customer requirement.
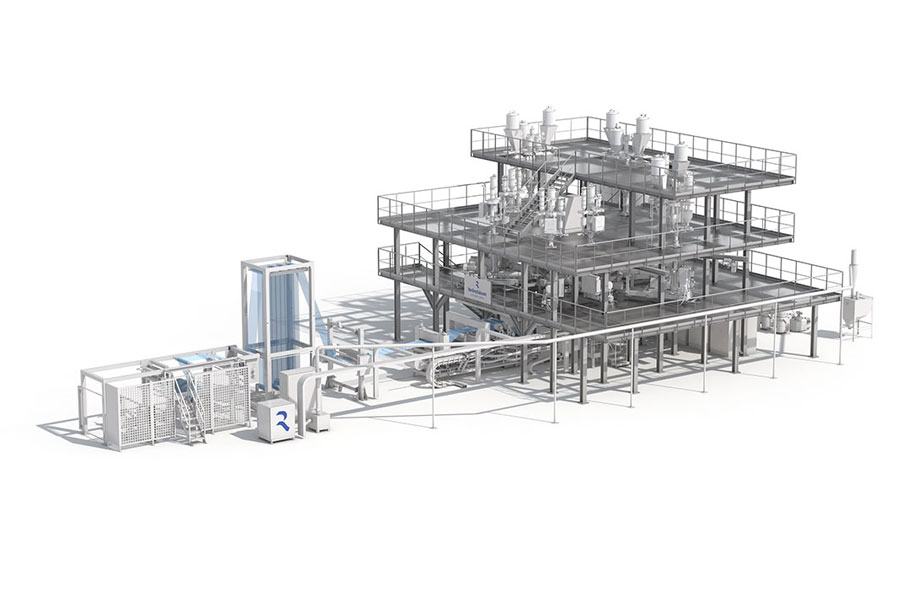
Polishing stacks for thermoforming film with excellent barrier properties.
Ensuring a secure global food supply is one of the most important challenges facing humanity. To achieve this, reducing food waste in the supply chain is essential.
Sophisticated and sustainable barrier films and packaging solutions play a key role in reducing food losses, ensuring hygienic packaging of sensitive goods, improving customer convenience and at the same time being as resource-efficient as possible.
With our advanced, fully integrated and automated Value Sheet barrier sheet systems, we offer the film and packaging industry a safe and proven solution.
The system concepts meet our customers’ requirements for reproducible and traceable quality with digital solutions for process and performance monitoring, but also with high-precision and reliable system components.
This starts with highly precise and reliable metering systems and is followed by wear-resistant and pressure-constant conventional multi-purpose and high-speed extruders for excellent melt quality, which ensure a constant supply to the core components of such a system – the co-extrusion feedblock and die.
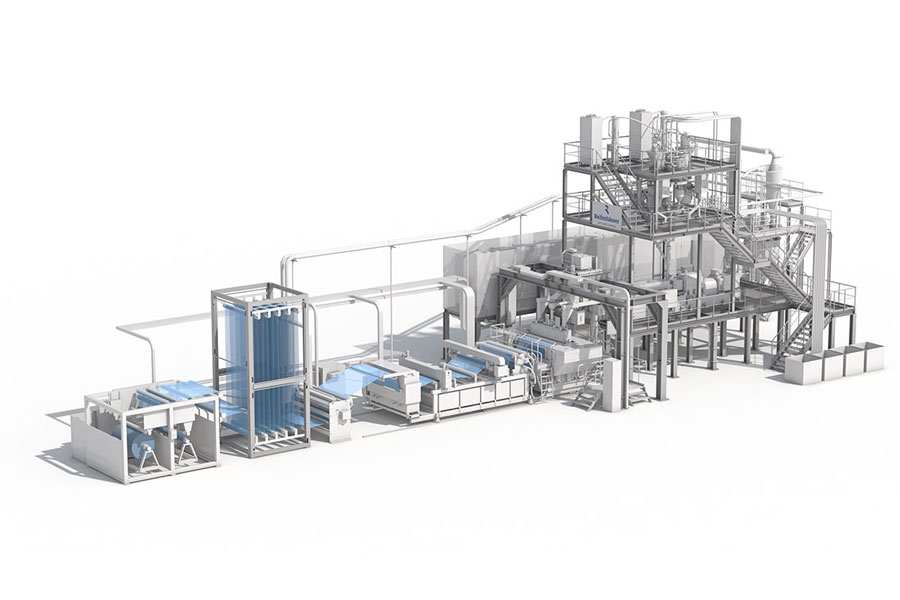
Special lines to produce film for the automotive/industrial sectors.
Films are used in a wide variety of applications in the automotive industry. From door panels to embossed cover films of a dashboard.
A melt is created from a plastic granulate via the extruder and then pulled apart via a flat die. In a subsequent smoothing process between two cooled rolls, the required film properties are finalized.
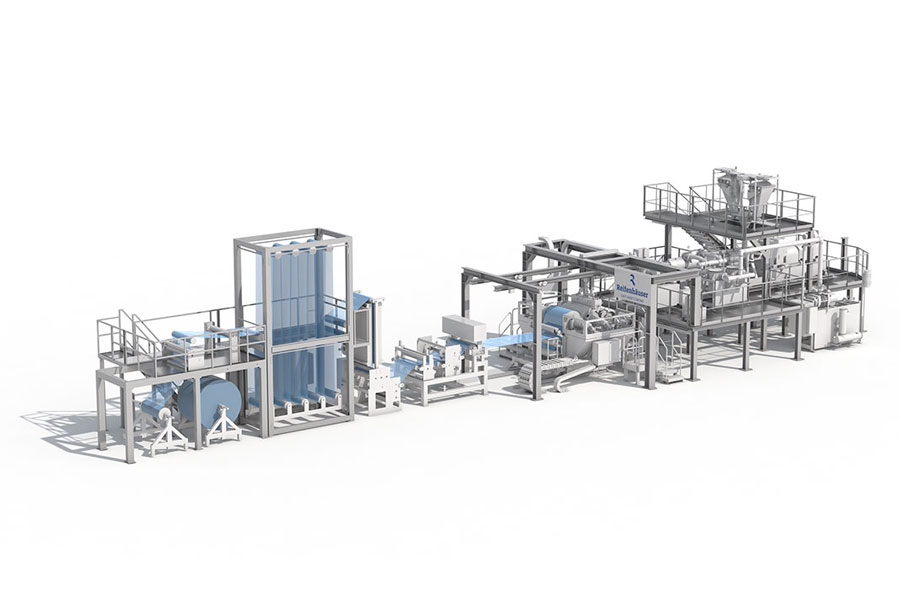
PET polishing stack with fast ROI, high OEE, and very short time to market.
PET is used for a wide range of applications: from food packaging to blisters and folding cartons.
The enormous range of requirements for film production often results in individual special solutions. The alternative is a modular concept, i.e. a construction kit with proven components. This is the basic idea behind our Value Systems. Value Lines feature Reifenhäuser’s proven quality. The use of tried-and-tested modules with high availability and perfectly coordinated project teams and processes ensure extremely short delivery and installation times.

Extrusion coating lines for composite films for various applications and industries.
From coffee packaging to truck tarpaulins, car headliners, construction film to medical and hygienic applications. Lamicor creates film composites as the optimal combination of a substrate material with a plastic coating.
The extruder in a Value Coating line produces a thermoplastic mixture from raw material, which is formed into a melt web by a slot die. This is permanently bonded to the substrate between the laminator roller and the pressure roller by pressure and heat.