Recycling
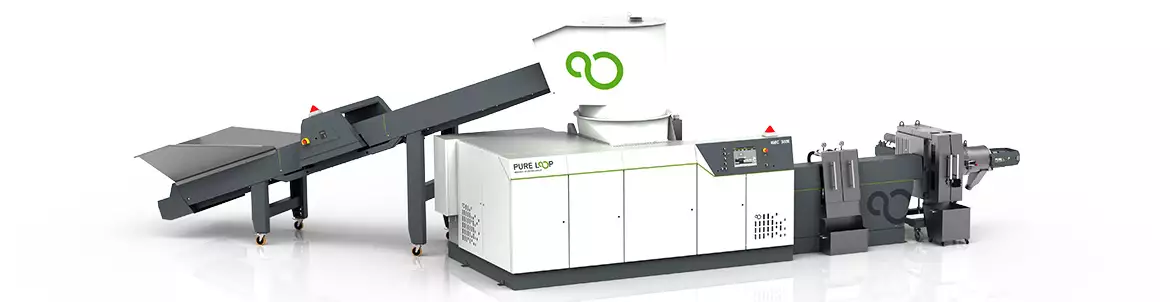
Plastics Recycling with Integrated Shredder-Extruder Combination
The PURE LOOP ISEC evo plastic recycling machine. It is powerful, easy to operate, cost-efficient and delivers more throughput.
The integrated shredder-extruder combination gently converts your production scrap into recycled plastic pellets. Whether handling heavy or light, high volume or high tensile strength, this recycling machine efficiently processes a wide range of industrial and post-industrial materials.
Material All-rounder
- The combination of a double feed ram system and single shaft shredder forms a unique technology. It guarantees high flexibility and makes the ISEC evo a material all-rounder.
Easy to Operate
- The innovative control system on the ISEC evo plastic recycling machine is really simple and convenient. The automatic features minimize operator requirements while ensuring a stable process and consistent quality.
Saving Energy & Costs
- The ISEC evo plastic recycling machine’s intelligent technology ensures that it operates in a power-saving way. As a result, your ongoing production costs are reduced.
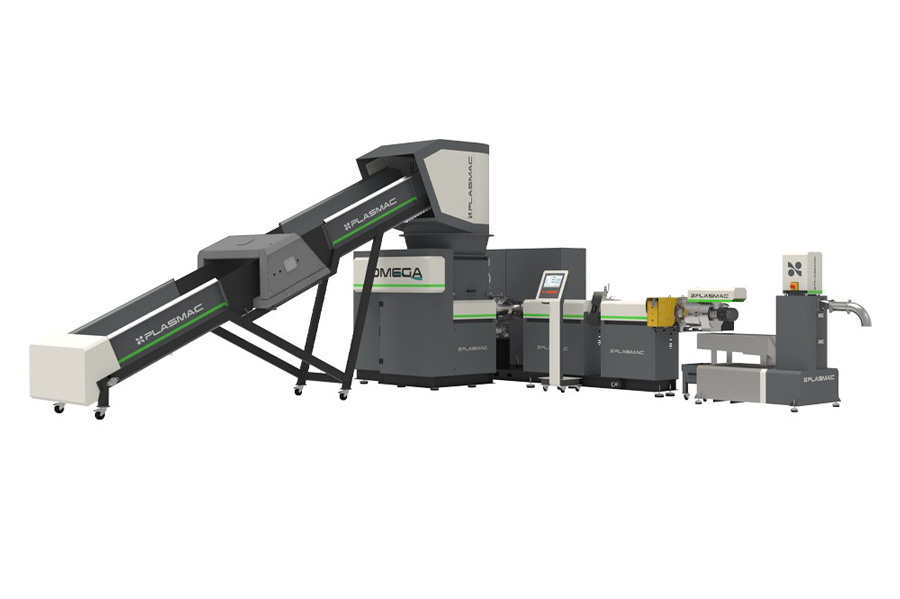
The OMEGA recycling shredder extruder system uses Plasmac’s unique dual diameter Short Screw Technology (S.S.T.).
The waste material is fed via elevator, rollfeed or trim basket into the slow rotating shredder, Plasmac’s unique screw design ensures minimal heat and dust meaning a higher quality pellet is generated with the lowest levels of gels possible. The S.S.T. ensures low shear, runs at low melt temperatures and therefore guarantees an absolute minimum of material degradation giving you the highest quality recycled pellet.
Advantages
- Minimal power consumption & the highest output / kW of installed power in the market. Giving you lower running cost and therefore the quickest return your on investment with paybacks in as little as six months.
- Low shear, minimum process dwell time and the absolute minimum of material degradation. Means you can recycle all of your scrap material into high quality pellets, reducing your material costs and improving your profitability.
- Slow rotating shredder technology and unique screen design. Requires no cooling water of the rotor or transfer system, reduces maintenance and costs, therefore improving your profitability.
- Smallest footprint recycling machine available on the market. Minimal floor space is required freeing up valuable floor space for other applications.
- ANCILLIARES AIR or WATER COOLED PELLETISER Air or water pelletisers, the material or output being run determine the type of pelletiser needed.
- TRIM BASKET For feeding inline trims into the shredder.
- REELFEED Used to feed off-spec or scrap reels into the shredder.
- ELEVATOR & METAL DETECTOR Used to convey loose, pieces, reels, lumps, in fact any type of scrap into the shredder.
- SCREEN CHANGERS Manual or automatic systems available, used when running offline products i.e. reels, flake etc.
- VACUUM DEGASSING STATION Single or double venting systems available to allow you to run printed or hydroscopic materials.
- DTEC A pellet detection system to advise if there are issues in the pelletiser.
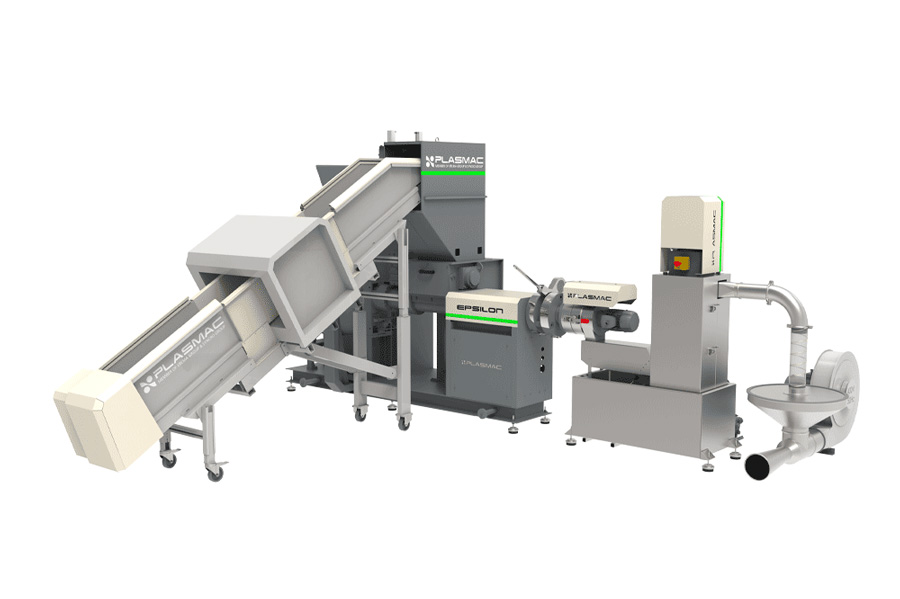
The EPSILON recycling inline shredder extruder system uses Plasmac’s unique Short Screw Technology (S.S.T.).
The waste material is fed via trim basket, rollfeed or elevator, in to the inline shredder, the size reduced material is then fed directly in to the feed throat of the extruder. No water cooling or compressed air is needed and the slow rotating shredder rotor ensures dust generation is kept to a minimum which means a higher quality pellet is produced with the lowest levels of gels possible. The S.S.T. ensures low shear, runs at low melt temperatures and therefore guarantees an absolute minimum of material degradation giving you the highest quality recycled pellet.
Advantages
- Minimal power consumption & the highest output / kW of installed power in the market. Giving you lower running cost and therefore the quickest return your on investment with paybacks in as little as six months
- Low shear, minimum process dwell time and the absolute minimum of material degradation. Means you can recycle all of your scrap material into high quality pellets, reducing your material costs and improving your profitability
- Slow rotating inline shredder technology and unique feed hopper design. Requires no cooling water of the rotor, reduces maintenance and costs, therefore improving your profitability
- Smallest footprint recycling machine available on the market. Minimal floor space is required freeing up valuable floor space for other applications
- TRIM BASKET for feeding inline trims into the recycling extruder.
- AIR or WATER COOLED PELLETISER: air or water pelletisers, the materials or output being run will determine the type of pelletiser required
- ROLLFEED Used to feed off-specification reels or scrap reels into the extruder, can be used simultaneously with the trim basket
- ELEVATOR Used to convey loose, slabbed, pieces and small lumps into the shredder
- SCREEN CHANGERS Manual or automatic systems available, used when running offline products i.e. reels, flake etc
- VACUUM DEGASSING STATION Single or double venting systems available to allow you to run printed or hydroscopic materials.
- DTEC A pellet detection system to advise if there are issues in the pelletiser.