Laminating
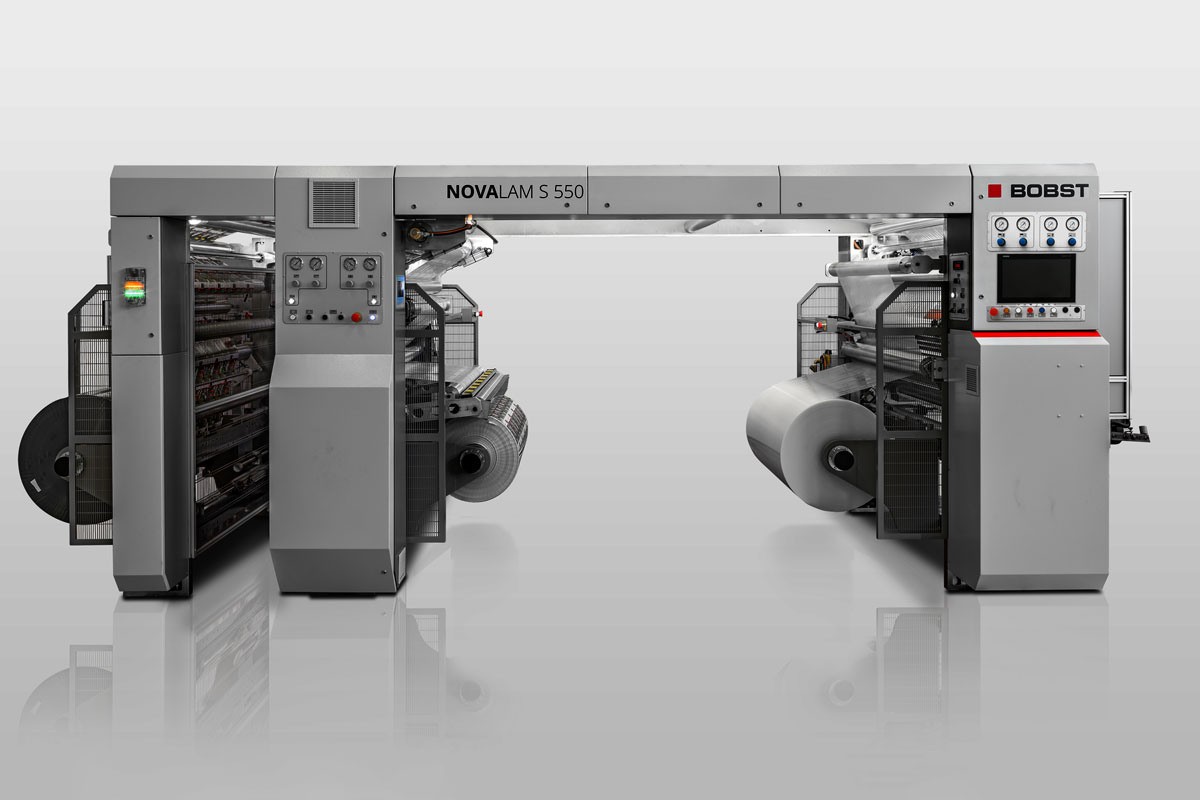
Versatile, flexible and ready to start
- Designed to handle a variety of substrates including thin alu-foil, metallized film and thin stretchable materials
- Equipped with sleeve transfer rollers for easy and fast job changeover
- Plug & play installation – no foundation needed, averages 1 week from arrival to production
- Standard web widths: 1030 – 1330 – 1530 mm. Other web widths available as option.
- Lamination speed up to 450 m/min
- 0 industry ready for post processing data.
Productivity & quality from short runs upwards
- Job changeovers completed in minutes without tools irrespective of configuration:
- on-board rotating cantilever system for sleeve type roll
- Pneumatic opening of metering roller for quick and easy adhesive disposal
- Automatic reel centering system reducing waste and start-up time:
- one touch winder setup
- quick fine tuning after web threading
- perfect reel alignment with linear encoder
- no telescopic effect
- Patented fully integrated automatic washing as standard supply
- 3-roller laminating nip for superior optical quality of coated adhesive
- 2 heated rolls for optimal process temperature control
- Independent setting of thermal regulation for coating unit and metering rolls.
Cost optimization and easy operation
- Patented design of long-life side retainers improves the laminator’s efficiency and decreases costs
- Layout enabling full accessibility to the laminating nip for quality and process inspection without stopping the machine
- BOBST adhesive mixer solutions for effective adhesive quantity control, matching production requirements
- Micrometric adjustment for perfect coating adhesive distribution
- Fully integrated HMI
- Intuitive, easy to read pictogram and commands for the setting, display and storage of individual job working parameters.
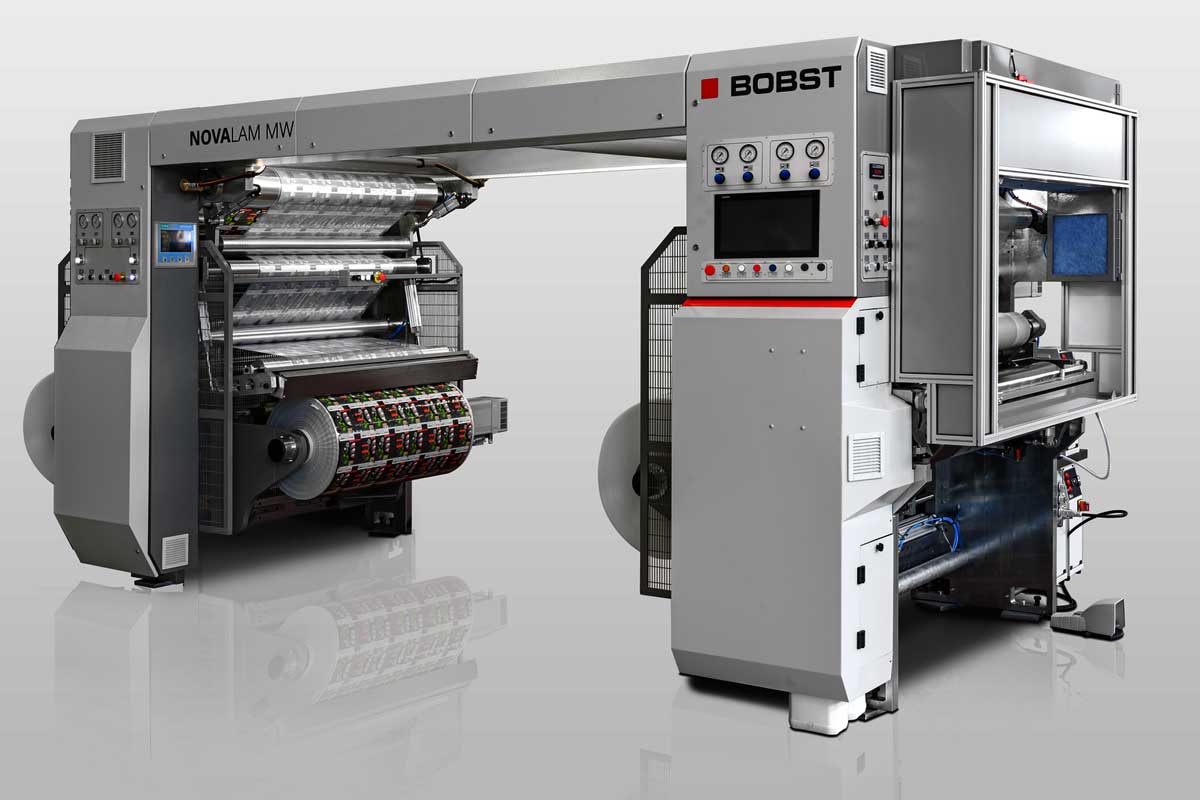
Compact, ready to start
- Optimized overall dimensions for limited footprint
- Web widths 830 mm. Ideal digital market solution
- Lamination speed up to 350 m/min
- Handles reels up to 1000 Kg
- Plug & play installation – no foundation needed, averages 1 week from arrival to production
- 0 industry ready for post processing data.
Cost optimization and easy operation
- The narrower-web design enables to optimize the efficiency of very short run productions
- Patented design of long-life side retainers improves the laminator’s efficiency and decreases costs
- BOBST adhesive mixer solutions for effective adhesive quantity control, matching production requirements
- Micrometric adjustment metering roller for perfect coating adhesive distribution
- Fully integrated HMI
- Intuitive easy to read pictograms, commands for the setting, display and storage of individual job working parameters.
Productivity & quality with ultra-short runs
- Designed to handle a variety of substrates including thin alu-foil, metallized film and thin stretchable materials
- Job changeovers completed in minutes without tools. On-board rotating cantilever system for sleeve type roll
- Pneumatic opening of metering roller for quick and easy adhesive disposal
- Available productivity-enhancing options:
- Patented fully integrated automatic washing
- Independent setting of thermal regulation for coating unit and metering rolls
- Cooling roller after laminating unit
- Coating thickness measurement system
- Anodized idle rollers.
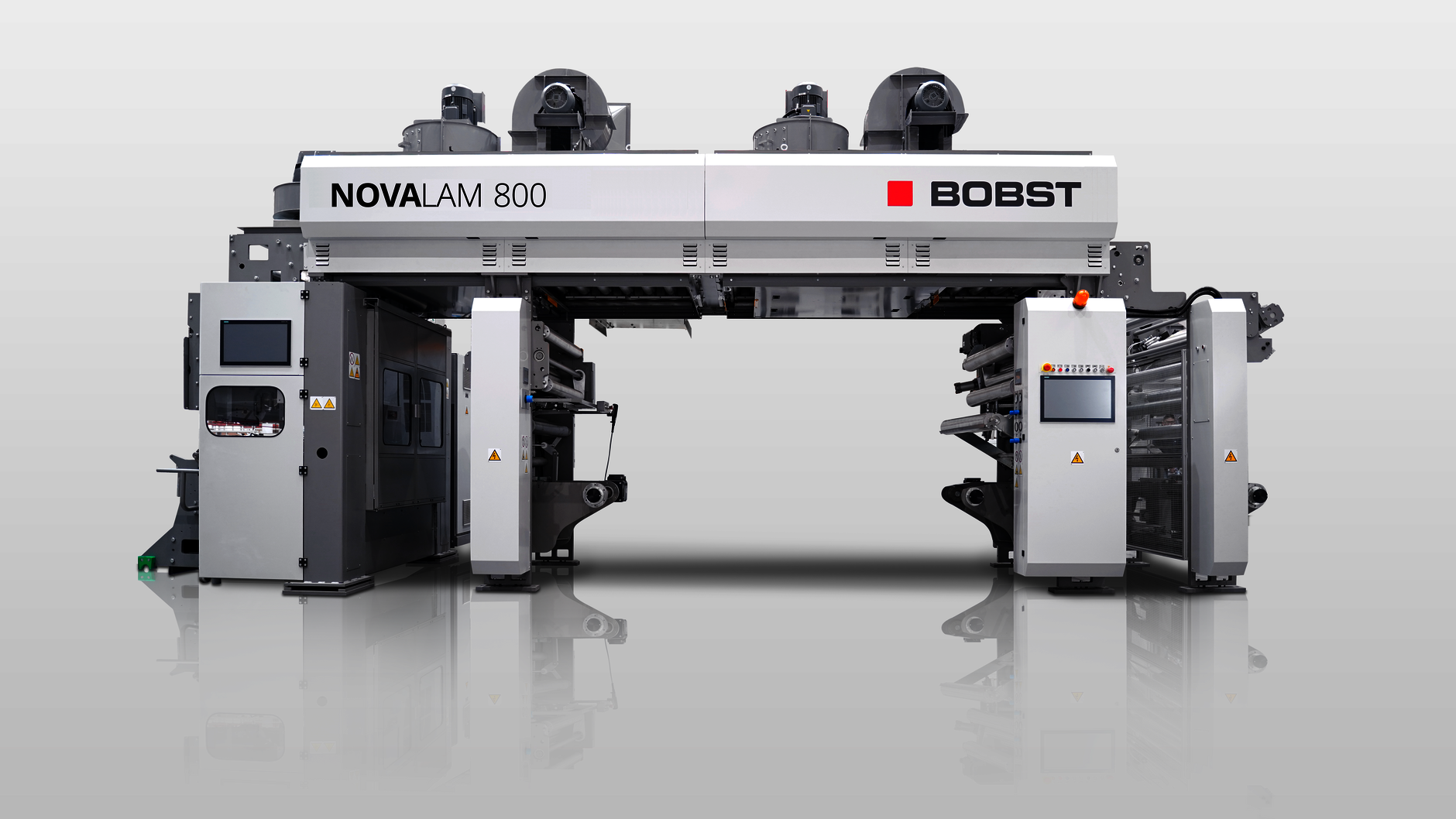
Compact, automated and connected
Compact design with lateral trolley extraction
The new NOVALAM 800 layout is characterized by a 4 colums design: two separating the coating section from the primary unwider, and two separating the bonding section and the rewinder from the secondary unwinder, granting:
Optimum accessibility for easier and faster web infeed
Easier and quicker cleaning and maintenance operations, considerably reducing machine downtime
Fully integrated HMI for setting, display and storage of individual job working parameters in easy to recall job recipes
The operator can easily and rapidly switch between jobs
Connectivity features for full production and quality control.
Superb product quality and sustainable operation
Very precise web handling on all substrates types, thicknesses and web combinations. Excellent performance at speed with critical substrates such as thin alu-foil, metallized films, and thin stretchable materials
New 3-roller laminating nip for enhanced optical quality of the laminate
Latest trolley design delivering coating uniformity and visual appeal with all applications
Flat drying tunnel and perfect web transportation by motorized rollers, avoiding breakages and scratches on critical substrates like alu-foil and metallized film
Unique cost saving solution of BOBST flexo trolley: less adhesive required and up to 50% less solvent
Motorized pressure roller for more accurate and uniform adhesive metering, ideal for multi-roller and reverse coating technology
Exclusive Registron® Mark-to-Mark reading technology for in-register cold seal coating and lacquer coating, enabling real time reading and detection of cold seal presence, avoiding costly non-conformities.
High flexibility and productivity
Designed to efficiently handle different film and paper substrates and consumables types: both conventional substrates and those designed for recycling
Highly productive from ultrashort run upwards
Multi-trolley design for different process technologies:
Solvent-based and water-based dry lamination
Solventless lamination
In register cold seal coating on pre-printed substrates
In-register printing of one additional color
Lamination speed up to 450 m/min.
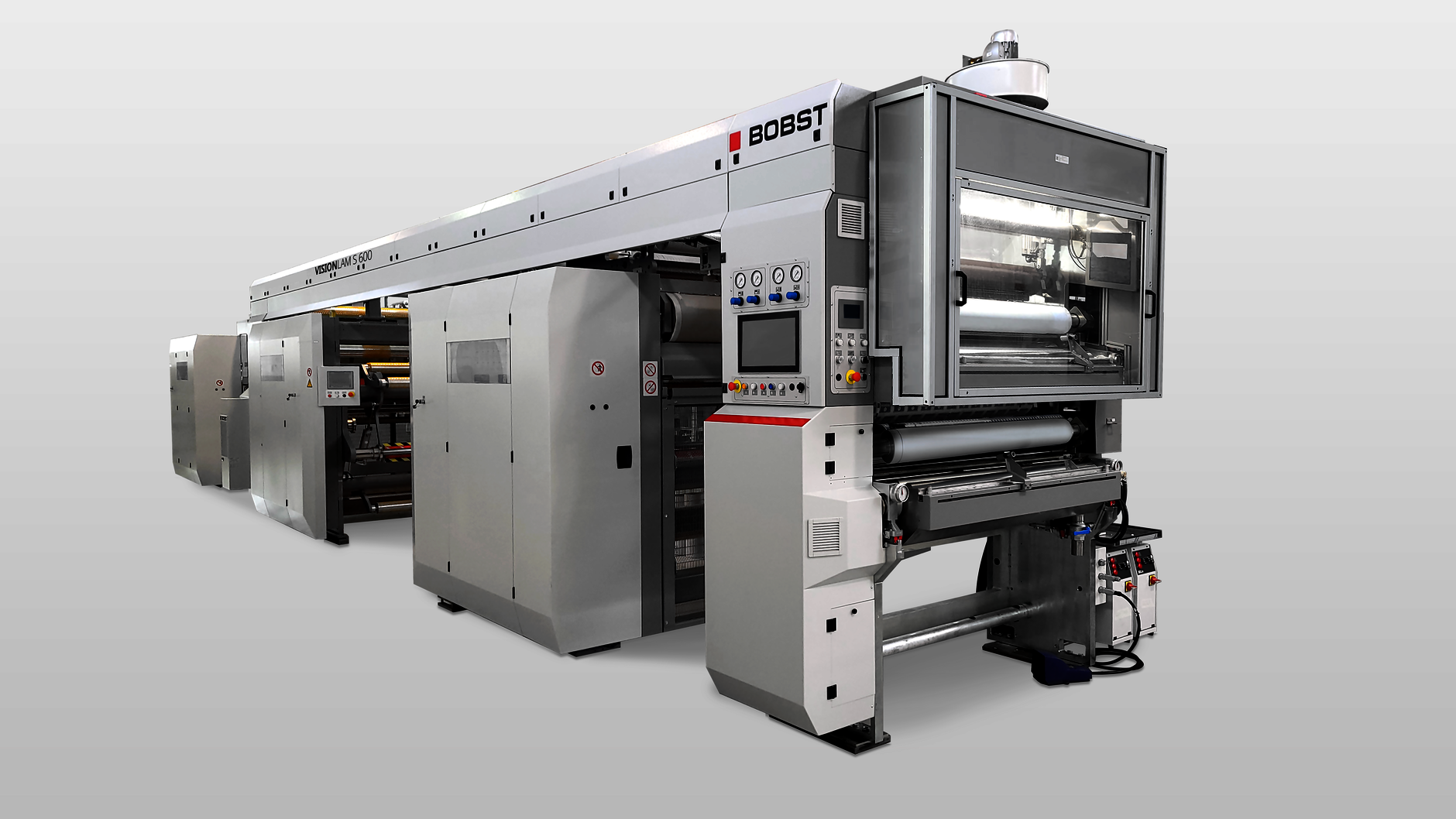
High substrate versatility
Highly precise control of web tension from rewind to unwind
Very accurate solventless system and unique design of the coating unit
Handles a variety of substrates including thin alu-foil, metallized film and thin stretchable materials for a wide range of applications
Fully automatic bi-directional reel splice
Production speed 450 m/min.
Exceptional product quality
Very accurate solventless system and unique design of the coating unit
Highly sensitive control of web tension from rewind to unwind
Excellent coating profile consistency.
Easy operation
Quick to set up
Easy and fast job changeovers without tools
Fully integrated HMI for setting, display and storage of individual job working parameters in easy to recall job recipes
Optimum accessibility for cleaning and maintenance
Connectivity features for full production and quality control.
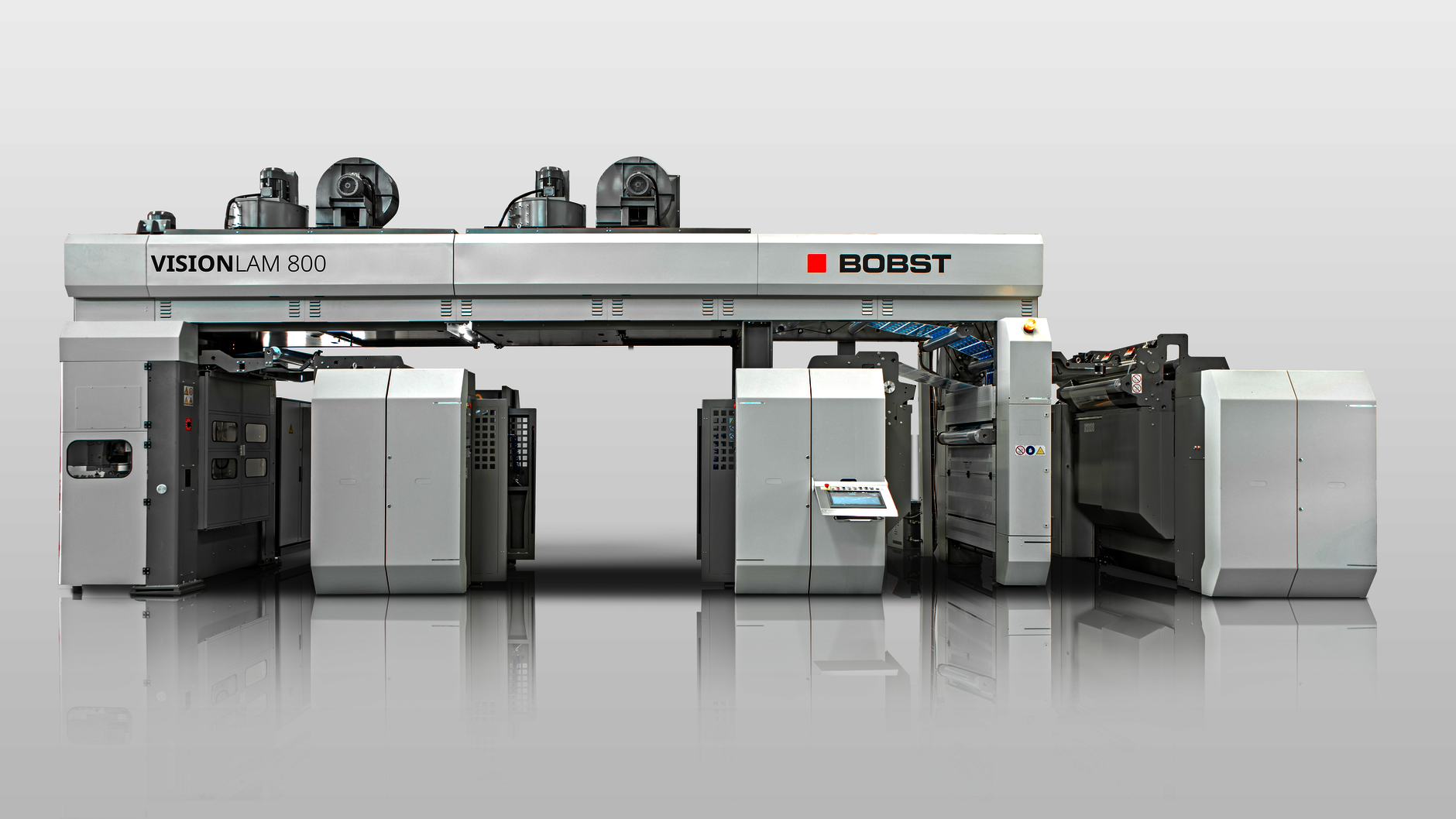
High flexibility and productivity
Handles a wide variety of film and paper substrate and consumable types, both conventional and those designed for recycling, at speeds of up to 450 m/min.
Multi-trolley design for different process technologies:
Solvent-based and water-based dry lamination
Solventless lamination
In register cold seal coating on pre-printed substrates
In-register printing of one additional color
Ideal configuration for efficient operation with minimum downtime for medium to long run production.
Premium product quality and efficient operation
Flawless lamination quality with all substrate types, thicknesses and web combinations. Excellent performance at speed with critical substrates such as thin alu-foil, metallized films, and thin stretchable materials
The optimal web transportation system by motorized rollers in the flat drying tunnel avoids breakages and scratches on critical substrates.
Widening and diversification of the converter’s applications thanks to the possibility to extend the tunnel length up to three sections, each with independently adjustable temperature. Solvent residue is minimized, the control of web tension is maintained
Latest trolley design delivering coating uniformity and visual appeal with all applications
Unique cost saving solution of BOBST flexo trolley: less adhesive required and up to 50% less solvent
Motorized pressure roller for more accurate and uniform adhesive metering, ideal for multi-roller and reverse coating technology
Exclusive Registron® Mark-to-Mark technology for in-register cold seal and lacquer coating, enabling real time reading and coating detection, avoiding costly non-conformities.
Operator-friendly, automated and connected
Operator-friendly design:
Lateral trolley extraction
Optimum accessibility for easy and fast web infeed
The operator can easily and rapidly switch between jobs
Easier and quicker cleaning and maintenance operations, considerably reducing machine downtime
Fully integrated HMI for setting, display and storage of individual job working parameters in easy to recall job recipes
Connectivity features for full production and quality control.
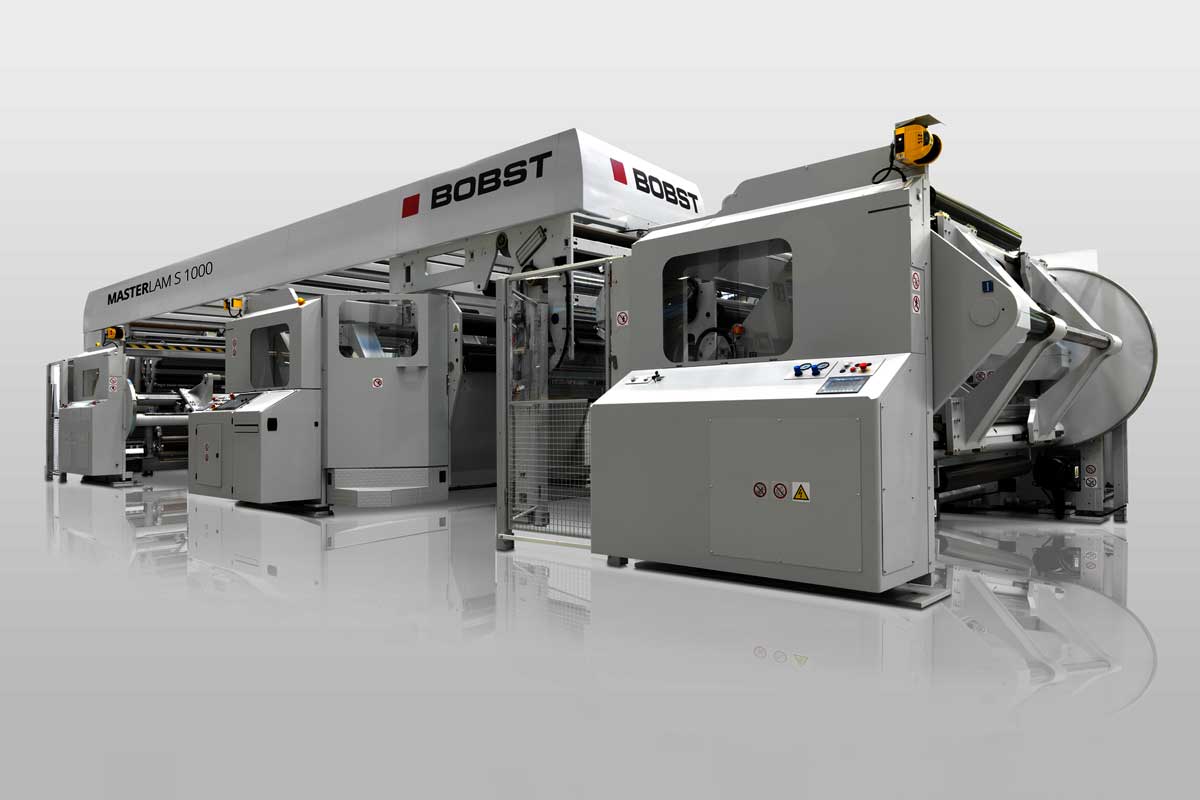
Exceptional flexibility
- Available in two different layouts to best fit production requirements
- Larger web widths up to 1750 mm and above upon request for industrial applications
- Customizable in terms of web width, winders and reel diameters.
- Perfect handling of different substrate types including thin alu-foil, metallized film and thin stretchable materials.
- High performance production speed up to 600 m/min.
Exceptional quality at high speed
- Very sensitive web handling on all substrates types, even at high speed
- Increased machine uptime.
Easy operation
- Quick to set up
- Easy and fast job changeovers without tools
- Fully integrated HMI for setting, display and storage of individual job working parameters in easy to recall job recipes
- Optimum accessibility for cleaning and maintenance
- Connectivity features for full production and quality control.